We Fix Leaking Masonry Parapet Walls
Leaking Parapet Walls with Capstones
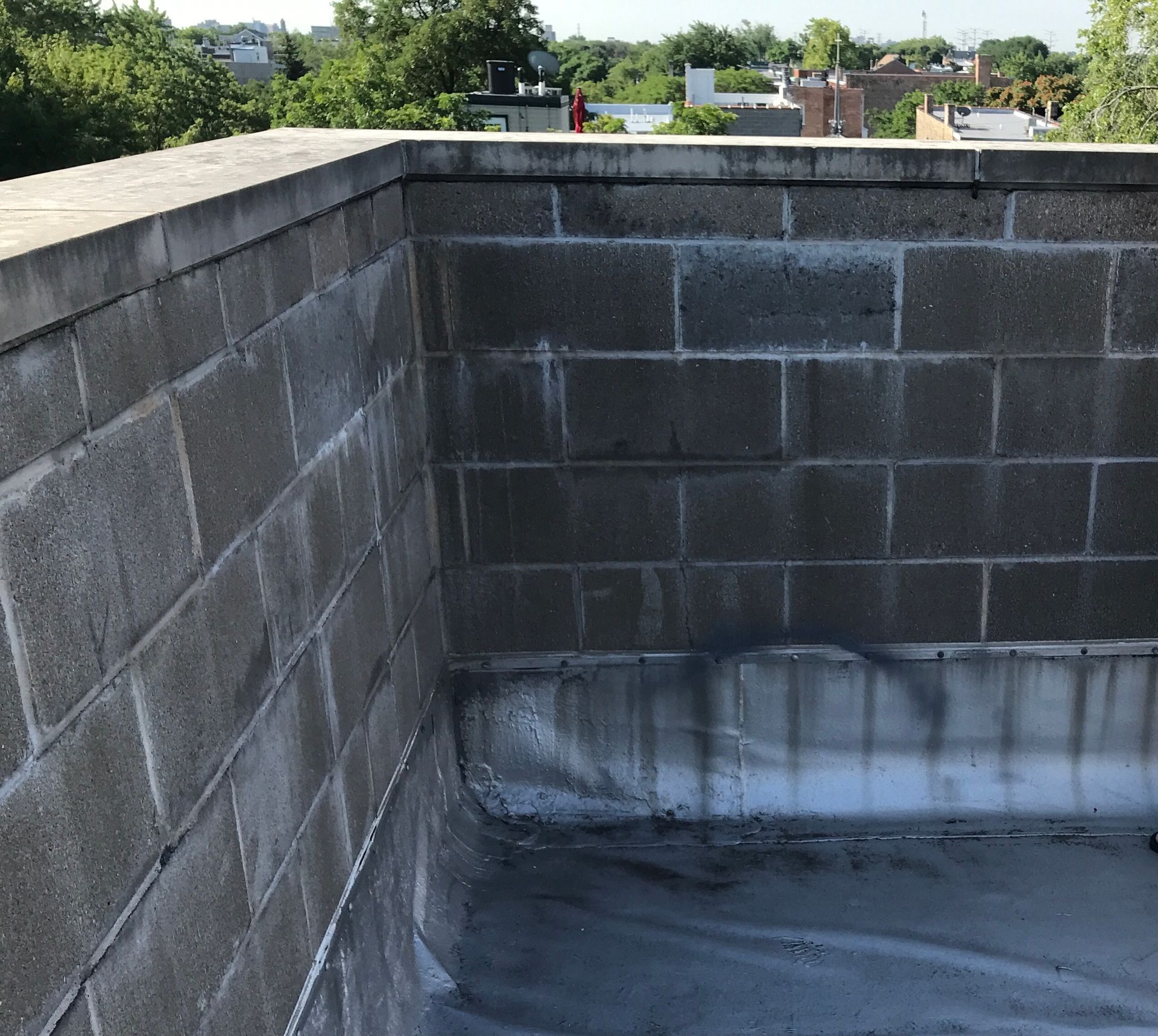
Obviously wet Split Face Block parapet with flat concrete capstone that has no overhang or drip groove in the stone, installed with no mason's flashing or metal drip edge in Wicker Park neighborhood of Chicago
Missing Mortar, Flashing and Drip Edge under Pre-Cast Concrete Capstone on leaking brick parapet wall in Chicago's Uptown neighborhood
Parapet walls, originally designed to conceal archers from invaders, have always been wet. In this century, the purpose of the parapet is decorative and to conceal rooftop mechanicals, like air conditioning units. Building owners with rooftop decks also benefit from the privacy and safety that parapet walls provide.
Unfortunately, parapet walls take a real beating from the weather, getting hit by wind driven rain and snow on all 3 sides - the interior, the exterior and the top. Historic (before 1980) building parapets are typically common brick and/or natural stone.
Contemporary parapets are typically Split Face Block or concrete block, some have a a brick facade with a block structural wall. Most contemporary parapets were built with mortar containing Portland cement which traps moisture.
Parapets built prior to 1980 are typically capped with limestone capstones or clay copings. Both installations leak, but they also breathe and allow moisture to escape. More contemporary parapets, built 1980 to present, may be capped with Renaissance Stone, which is pre-cast concrete, metal copings, clay coping tiles or coping tiles that look like clay.
Renaissance Stone and Concrete Capstones
Contemporary "natural" looking capstones leak like sieves. We have found capstones that are not manufactured to industry standards – for example – capstones that are flat on top vs. pitched to one side to shed rain water quickly.
We have also found capstones that do not have a drip groove or channel – this recess on the bottom of the capstone breaks the surface tension of water rolling down the vertical edge of the stone. This groove, sometimes call a throat in stone work, prevents water from running down the face of the wall and from migrating into/toward the wall.
In addition, actual installation methods cause water intrusion. We see wet walls everyday where common mason's flashing and/or metal drip edge is not installed properly under the capstones. And sometimes, no flashing is installed under the capstones. These wall may as well be open to the sky.
Click here to learn more about Leaking Renaissance Stone capstones and decorative details
Leaking, Wet Parapet Walls with Metal Copings
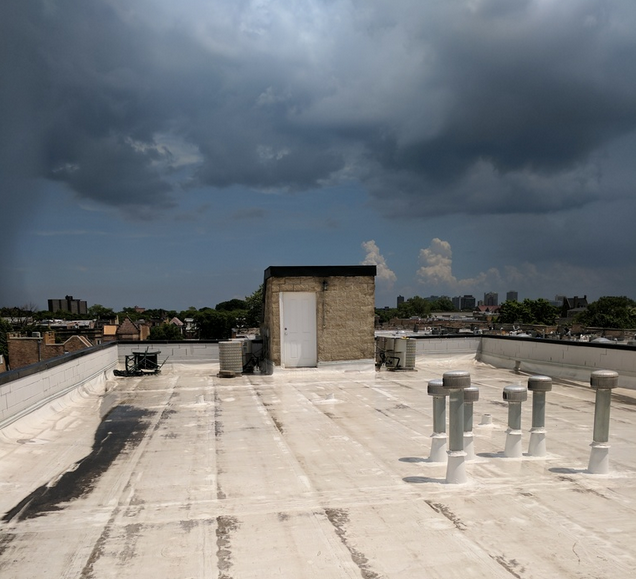
Short legs on metal coping contributed to the moisture issues on this Split Face Block building in the Grand Boulevard neighborhood of Chicago
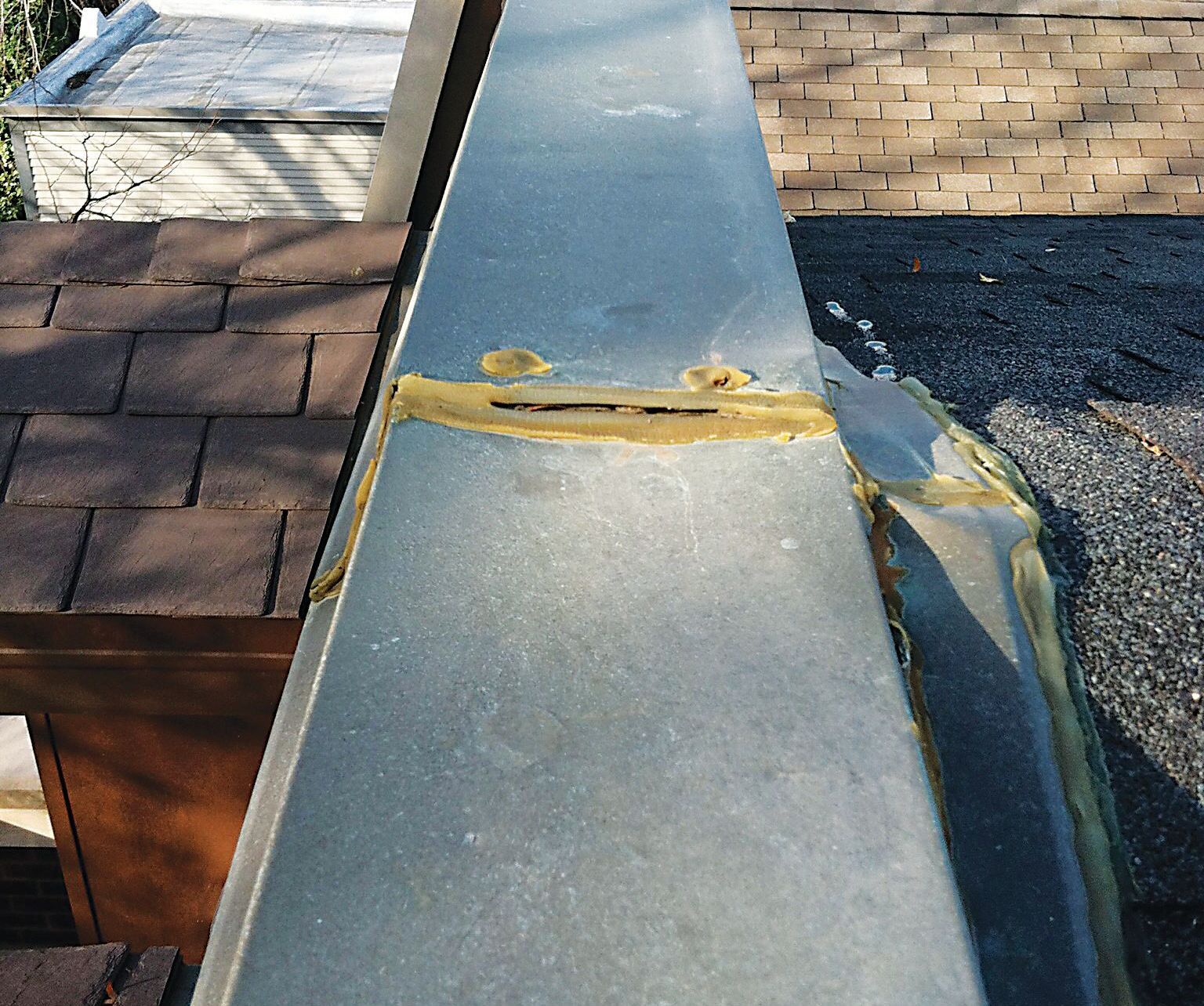
Flat metal coping with short legs, installed with insufficient overlap between coping lengths and failing caulk joint allows a significant amount of rain into the wall – Lakeview neighborhood, Chicago, IL
Best Practices for Metal Copings
Metal copings, if designed with long enough legs on the exterior and interior sides, and installed properly, do keep moisture out – but metal copings also keep trapped moisture in the walls.
Metal coping legs should be no less than 4" to properly protect the top of the parapet wall from wind-driven rain. The coping should also be sloped to the interior (roof side) to direct rain, snow and ice away from sidewalks, etc. A flat coping can allow water to sit on top, and over time that water can erode the coping or find its way into the coping and wall via seams in the coping.
It's said that every 1" of coping leg protects against 15 mph of wind-driven rain. We see flat, 3" coping legs on wet parapet walls everyday. The reason this theory doesn't hold water - is that the "best practice," (translation – the way its always been done) installation method in Chicago is to bolt/screw/nail/glue a 1.5" thick piece of pressure treated lumber to the top of the parapet and then attached the metal coping to the lumber.
We remove copings on a regular basis that are no longer attached to a lumber nailer – because the builder "value engineered" the pressure treated lumber out of the equation and used a regular piece of lumber that has now rotted away.
Doing the math – if a 3" coping leg is covering a 1.5" piece of wood, then the top of the parapet wall has only 1.5" of protection. So, the wall is only protected from a 22.5 mph wind-driven rain. If you live in Chicago, you know that a 30 mph wind during a storm is common place.
We always make copings with a 5" leg (minimum) on the exterior side of the wall to accommodate the pitch toward the roof (so snow slides off), and a 4" leg (minimum) on the interior side of the parapet wall to protect against a 60 mph wind-driven rain. The average wind speed in Chicago is 10.3 mph. The highest wind gust – 84 mph – in 30 years was recorded on July 14, 2022. Prior to that a gust of 70 mph was recorded on June 22, 2011.
That said, if your builder specified short legs (cut costs) on your metal coping, it is a likely source of moisture intrusion. In addition, metal copings are typically 10 feet long, the connection between copings, as well as the corners are typical water entry points. Regular maintenance of caulk joints is necessary, as caulk typically has a useful life of 5 years.
Leaking, Wet Parapets with Clay Coping Tiles
Real clay coping tiles with failing mortar joint at the junction in Edgewater neighborhood of Chicago, IL
Interesting Information on Clay Coping Tiles
Fired clay coping tiles date back to before Christ - yes BC. They are a near perfect parapet cap if manufactured and installed properly.
Unfortunately, depending on the age of your building, your "clay" coping tiles could be cement or a composite of asphalt and other stuff slapped together with Portland cement based mortar.
Surprise! The new copings coupled with new mortar don't perform as well as the tried and true real clay tiles set with lime/sand mortar. The good news is real clay coping tiles are available if you need to replace broken tiles or want to replace your "new and improved" coping tiles. Clay coping tiles of all kinds do break occasionally and need to be replaced. Regular maintenance is essential because broken tiles can allow a significant amount of water leak into the wall.
We fix wet parapet walls by installing WickRight Passive Ventilation® between the cap (capstone, metal coping or clay coping) and the parapet wall. We also apply masonry sealants to the walls to prevent moisture absorption.